UK Home Insulation: The R Value Facts You Need to Know
UK Home Insulation: Learn the R-value facts for energy efficiency. Boost comfort and cut energy bills with high R-value insulation today.
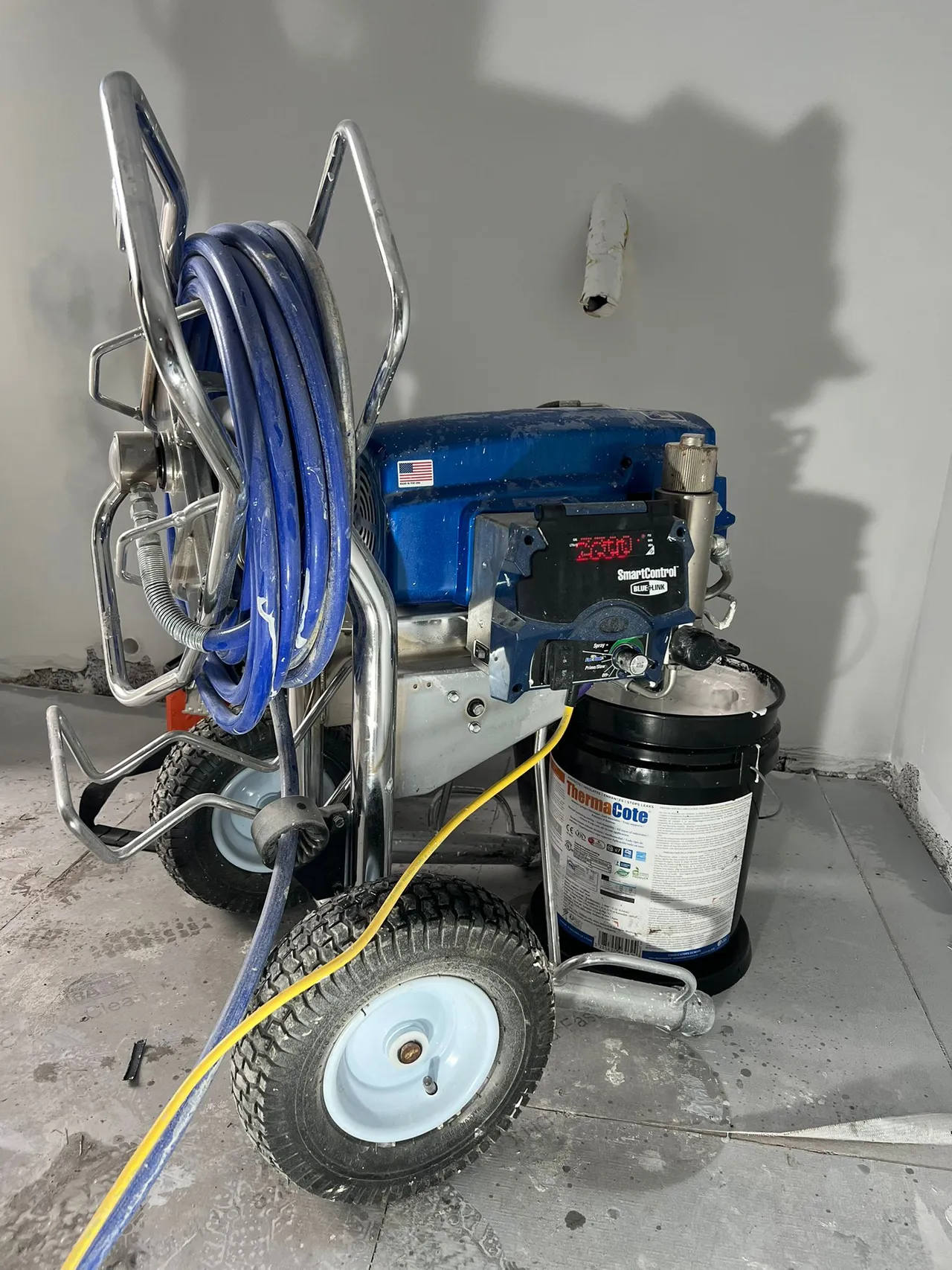
When winter arrives in the UK, so does the heating bill shock. In the cold months of 2025, many UK homeowners will waste hundreds of pounds through poor insulation – money that could stay in their pockets with the right knowledge.
R-value might sound like technical jargon, but it's actually the key to comfort and savings in British homes. This simple measurement tells you how effectively your insulation stops heat from escaping your home during those bitter UK winters – and prevents it from creeping in during increasingly hot summers.
Most UK homeowners don't know their home's R-values, and this knowledge gap costs them dearly year after year. With energy prices remaining high in 2025, this oversight is more expensive than ever.
The difference between adequate and excellent insulation isn't only about comfort – it's financial. A properly insulated attic can save the average UK household £250-£350 annually.
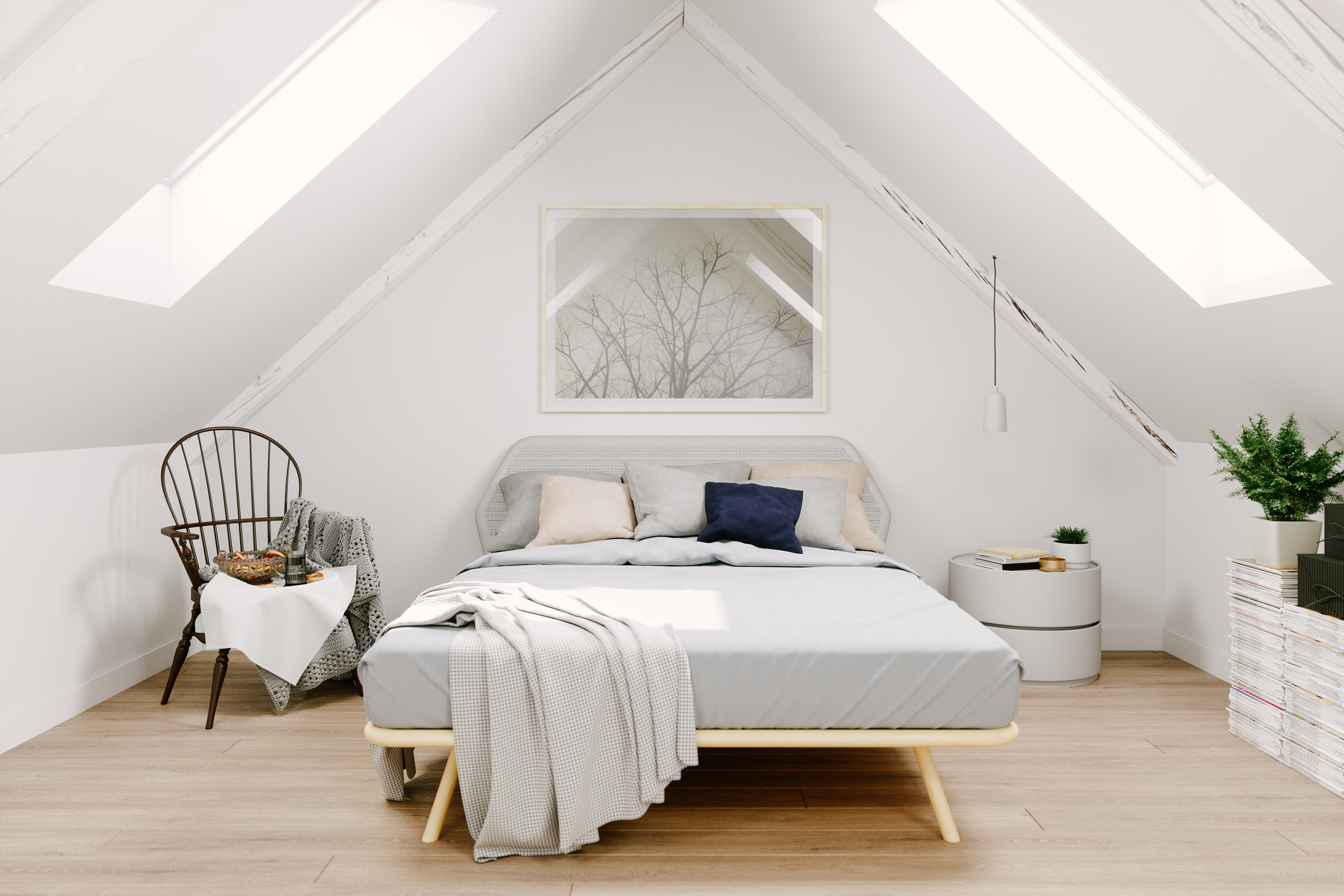
Over ten years, that's enough for a holiday abroad or a substantial home improvement.
But R-values aren't one-size-fits-all. The right values for a cottage in Cornwall differ from those needed for a semi-detached in Scotland. Location, home construction, and even which room you're insulating all matter.
Why should you care about R-values now? Because understanding them is the first step toward a warmer, more efficient home – and a significant reduction in those eye-watering energy bills.
What is R-value in UK home insulation?
- R-value measures thermal resistance in insulation materials
- Higher numbers mean better heat retention
- Critical for energy efficiency and comfort in UK homes
Examples of R-value in action
R-value measures how well insulation materials resist heat flow. In practical terms, it tells you how effectively your insulation keeps warm air inside during winter and outside during summer. The higher the R-value, the better the material is at stopping heat transfer.
In the northern regions of the UK like Scotland, where winters are particularly harsh, homes often require insulation with higher R-values compared to the milder southern regions. For instance, a typical home in Aberdeen might benefit from attic insulation with an R-value of R40 or higher to combat the cold temperatures and strong winds. This higher R-value creates a more effective thermal barrier against the severe winter conditions.
"An R-value measures how well a material resists heat flow. Think of it as a 'resistance score'—the higher the R-value, the better the insulation is at stopping heat from passing through." Source: PD Rendering
Types of R-value measurements
R-values are specific to different insulation materials, and each material has its own thermal resistance properties. Fibreglass batts typically have R-values between 2.2 and 2.7 per inch of thickness, while spray foam can reach R-values of 3.7 to 6.5 per inch. Stone wool insulation offers R-values around 3.0 to 3.3 per inch, making it a popular choice in the UK for its fire resistance and sound dampening properties.
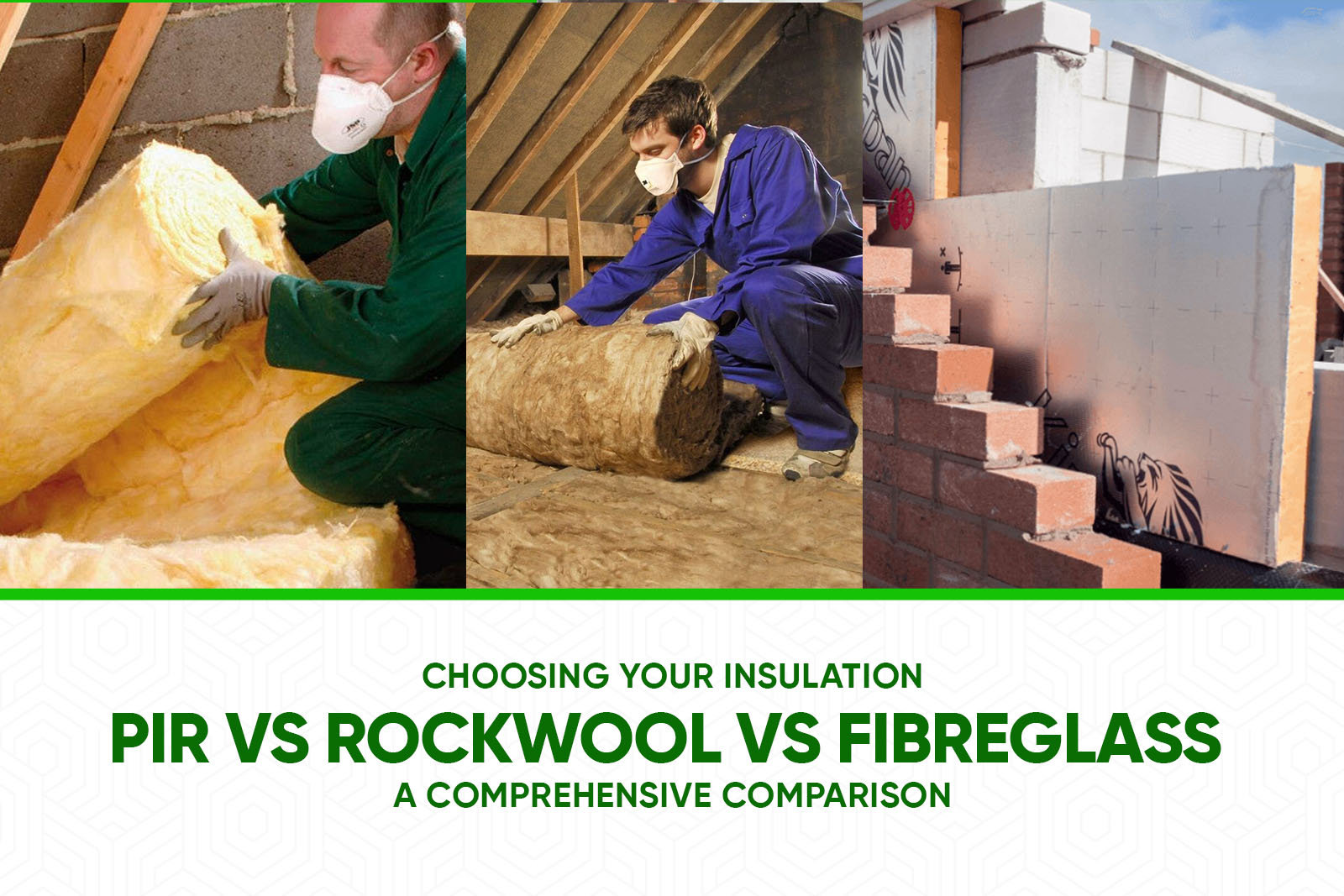
This Comparison Shows Conventional Insulation Types
When comparing R-values, it's important to note that the measurement scale used in the UK differs from the one used in the United States. The UK traditionally uses metric units (m²K/W), while the US uses imperial units (ft²·°F·h/BTU). A rough conversion factor is that 1 m²K/W equals approximately 5.68 ft²·°F·h/BTU. This difference can cause confusion when reading product specifications or international building standards.
The scoring of the R-value can range on a scale from 0 to an indefinite number. A higher score means a better 'resistance' to heat transfer.
- The truth is that R‑value starts at zero and increases indefinitely with added insulation.
- Saying “higher R‑value means better resistance” is correct (R higher = more thermal resistance) – but the upper limit of 66 commonly quoted is not a built-in constraint, just a common benchmark.
This range provides homeowners with a clear scale to assess insulation effectiveness across different areas of their homes, from minimal insulation at the lower end to super-insulated passive houses at the higher end of the scale.
Type 1: Attic insulation
Attic insulation in UK homes typically requires R-values ranging from R30 to R44. This higher range is necessary because heat naturally rises, making the attic a primary area for heat loss. An uninsulated or poorly insulated attic can account for up to 25% of a home's total heat loss, making proper attic insulation one of the most cost-effective energy improvements.
For homes in the northern UK, R-values closer to R44 are recommended to combat the colder climate. In central and southern regions, R-values of R30 to R38 often provide sufficient insulation. The UK's Building Regulations typically require minimum attic insulation levels equivalent to around R30, though this varies based on the specific construction type and region.
The installation method also affects the actual performance of attic insulation. Properly installed insulation with no gaps or compression achieves its rated R-value, while poor installation can reduce effectiveness by up to 30%. This is why professional installation is often recommended for attic spaces, especially when aiming for higher R-values.
Type 2: Wall insulation
Wall insulation R-values in UK homes typically range from R13 to R23, depending on the construction type and materials used. Solid walls, common in older UK properties, often require external or internal insulation systems with R-values of at least R13 to meet modern energy efficiency standards. Cavity walls in newer homes can achieve R20 or higher when properly filled with insulation material.
"Selecting the right R-value for insulation is essential for achieving energy efficiency, comfort, and compliance with building regulations. In the UK, aiming for R-values around 3.30 m²K/W for walls and above 4.54 m²K/W for roofs is advisable."
This guidance (approximately R19 for walls and R26 for roofs in imperial units) provides a good starting point for UK homeowners considering insulation upgrades.
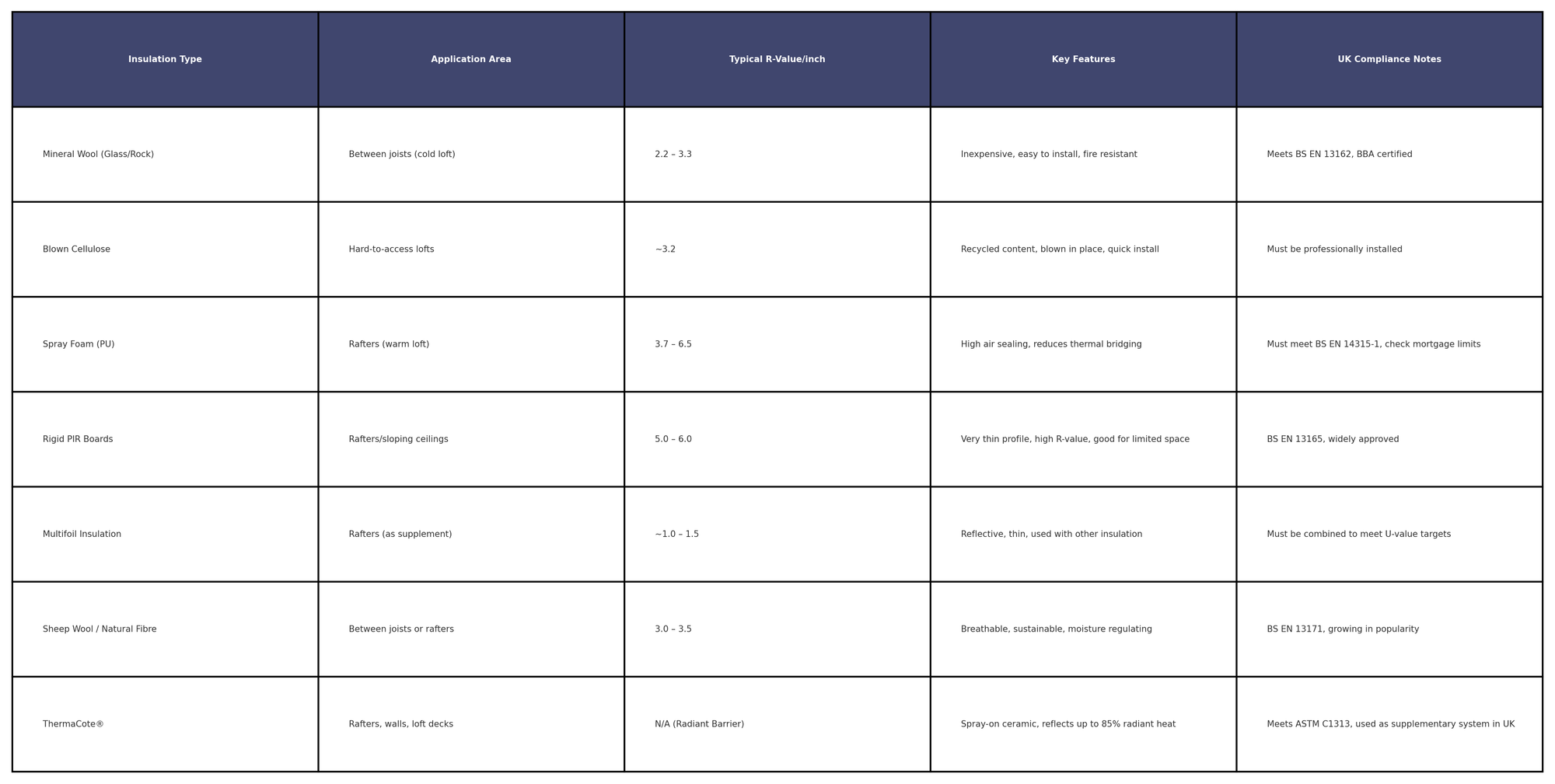
Wall insulation plays a crucial role in maintaining consistent indoor temperatures. Without adequate wall insulation, homes experience more significant temperature fluctuations, drafts, and cold spots. A well-insulated wall with an appropriate R-value acts as a thermal buffer, slowing heat transfer between the inside and outside of the home.
This results in more stable indoor temperatures, reduced strain on heating systems, and lower energy costs.
For period properties with solid walls, internal wall insulation with an R-value of R15 can reduce heat loss through walls by up to 60% while preserving the external appearance of the building.
Benefits of high R-value insulation
- High R-value insulation reduces energy bills by up to 30% in solid-walled homes
- Creates more stable indoor temperatures, eliminating cold spots in winter and heat buildup in summer
- Provides substantial return on investment through long-term energy savings and increased property value
When it comes to home insulation, R-value is the key measurement that determines how effectively your insulation resists heat flow. Higher R-values mean better insulation performance—a critical factor for UK homeowners facing rising energy costs and increasing climate unpredictability. The benefits of investing in high R-value insulation extend far beyond simple energy savings, though that remains a primary advantage.
Benefit 1: Lower energy bills
The most immediate benefit of high R-value insulation is the significant reduction in energy costs. Research from Leeds Beckett University found that properly insulating solid-walled homes—which make up about eight million households in the UK—can reduce energy bills by up to 30% annually.
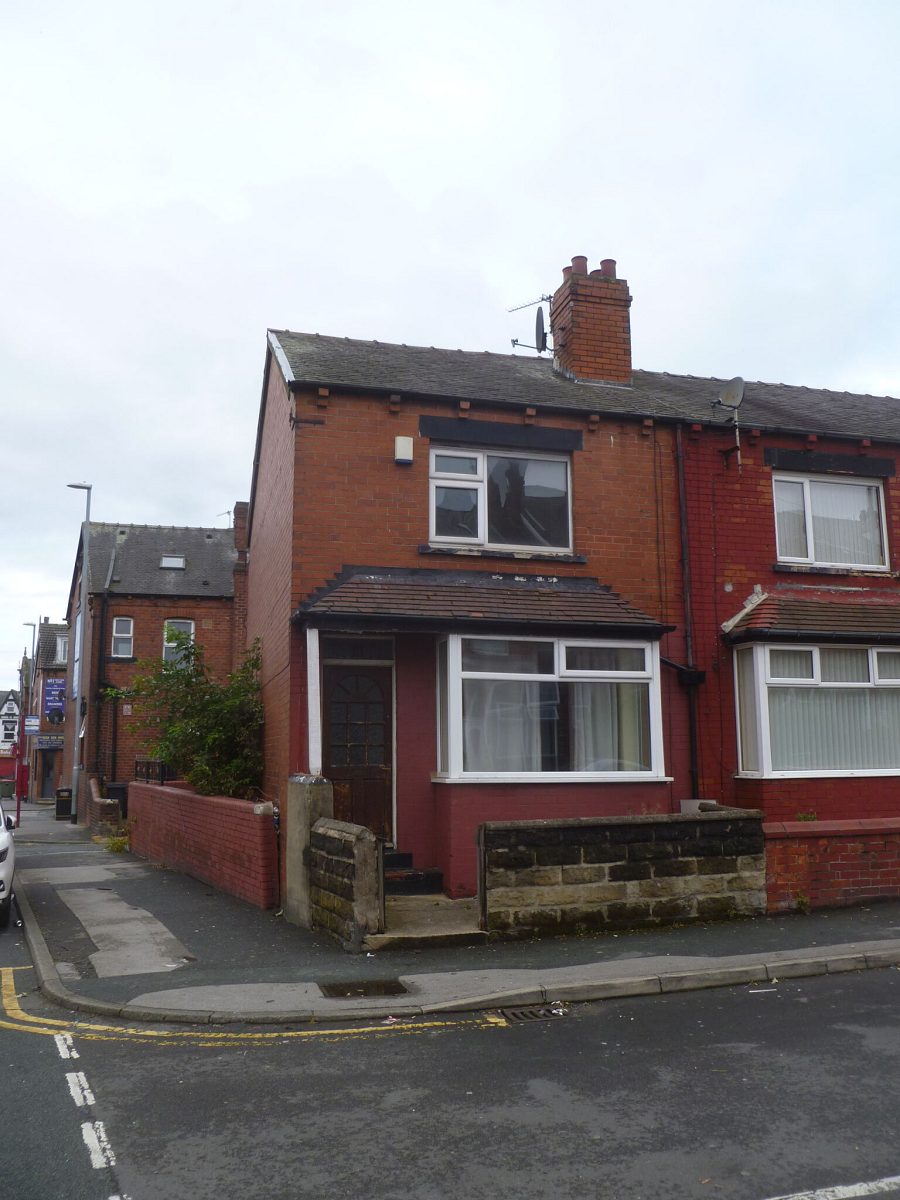
For the average UK household spending £1,200 yearly on heating, this translates to potential savings of £360.
The physics behind these savings is straightforward. When your home has better thermal resistance (higher R-value), less heat escapes in winter and less enters in summer. This means your heating and cooling systems work less, consuming less energy.
As Bradley Hirst, from Knauf Insulation say's in this piece;
"When insulating a building, the higher the R Value, the better. This is because less heat will escape, which ultimately reduces utility bills."
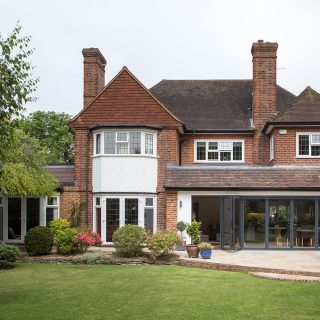
Cost-benefit analysis for different property types
The financial benefits of high R-value insulation vary based on property type and current insulation status. For older properties with solid walls and minimal existing insulation, the return on investment can be particularly impressive:
- Victorian terraced houses: Often see payback periods of 5-7 years for external wall insulation
- 1930s semi-detached homes: Typically recover costs within 6-8 years
- Modern homes with cavity walls: May see returns in 3-5 years when upgrading from basic to high-performance insulation
For a deeper understanding of the financial benefits, the book "Energy Efficiency in Buildings: CIBSE Guide F" provides comprehensive data on payback periods and energy savings across different UK building types.
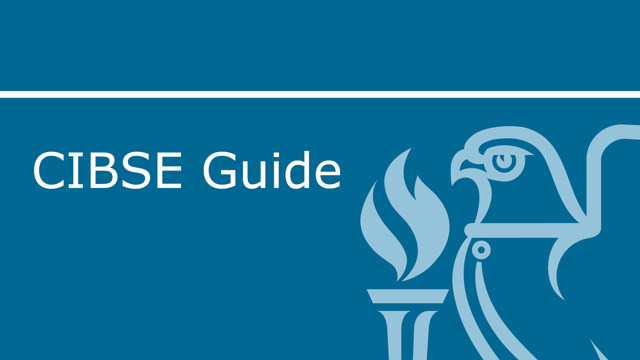
Benefit 2: Improved home comfort
Beyond financial savings, high R-value insulation transforms the living experience within a home. Poor insulation creates uncomfortable temperature variations—cold spots near exterior walls and windows in winter, and overheated spaces in summer. High R-value insulation eliminates these problems by creating a more uniform thermal envelope.
The Leeds Beckett University study reported that homes with upgraded insulation
"feel warmer in winter and cooler in summer,"
while also experiencing better air quality and reduced condensation. This balanced temperature not only improves comfort but also has health benefits, particularly for vulnerable populations like the elderly and young children.
Temperature stability is perhaps the most noticeable comfort improvement. Without adequate insulation, UK homes often suffer from rapid temperature fluctuations, especially during weather changes.
Benefit 3: Environmental impact reduction
High R-value insulation delivers substantial environmental benefits by reducing overall energy consumption. The UK's residential sector accounts for approximately 15% of the country's carbon emissions, with heating responsible for the largest share of this environmental footprint.
A well-insulated home with high R-values can reduce carbon emissions by 1-2 tonnes per year for the average UK household. This reduction comes from decreased energy consumption for heating and cooling, which directly translates to lower carbon emissions from fossil fuel-based energy sources.
The environmental benefits extend beyond carbon reduction. Less energy consumption means:
- Reduced demand for natural resources used in energy production
- Lower air pollution from burning fossil fuels
- Decreased pressure on the national energy grid during peak demand periods
For homeowners concerned with sustainability, the book "The Whole House Book: Ecological Building Design and Materials" by Pat Borer and Cindy Harris offers excellent insights into how high-performance insulation fits into broader ecological building strategies.
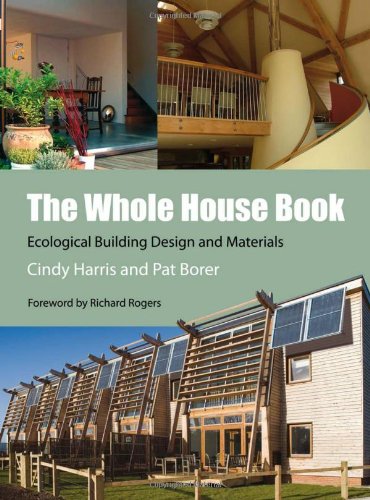
Benefit 4: Noise reduction and improved acoustics
An often-overlooked advantage of high R-value insulation is its acoustic performance.
Mark Bowman Explains Acoustics and Insulation
Many insulation materials that provide excellent thermal resistance also offer substantial sound dampening properties. This dual benefit is particularly valuable in urban areas or homes near busy roads, where external noise can be a significant issue.
Materials like mineral wool and foam insulation with high R-values can reduce sound transmission by 30-45 decibels, depending on installation quality and material thickness. This reduction can transform a noisy environment into a peaceful one, improving sleep quality and overall well-being.
The acoustic benefits vary by insulation type:
- Fiberglass insulation: Provides moderate sound absorption with R-values of 2.2-3.8 per inch
- Mineral wool: Excellent sound dampening with R-values of 3.0-3.3 per inch
- Spray foam: Superior acoustic performance with R-values of 3.7-6.5 per inch
For homes in noisy environments, choosing insulation materials that optimize both R-value and sound reduction creates a double benefit—energy efficiency and acoustic comfort.
Benefit 5: Increased property value and marketability
High R-value insulation represents a tangible investment in a property that pays dividends when selling or renting. Energy-efficient homes command premium prices in the UK property market, with studies showing that properties with high Energy Performance Certificate (EPC) ratings sell for 5-14% more than equivalent properties with poor energy efficiency.
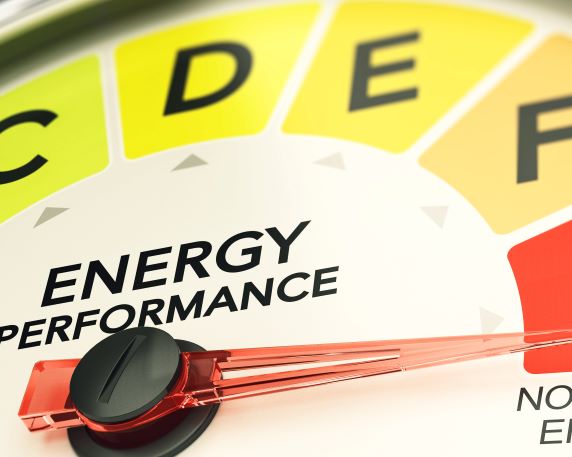
The UK government's push toward net-zero emissions by 2050 is already influencing property values. Homes with high-performance insulation and better EPC ratings have become more attractive to buyers and renters who understand the long-term cost implications of energy-inefficient properties.
Real estate data shows:
- Properties with EPC ratings of A or B sell 17 days faster on average than those with lower ratings
- Rental properties with high energy efficiency command 5-10% higher monthly rents
- Mortgage lenders increasingly offer preferential rates for energy-efficient properties
This value-add aspect of high R-value insulation means the initial investment is not only recovered through energy savings but also through increased property value—creating both immediate operational savings and long-term asset appreciation.
For property investors looking to maximize returns, the book "Sustainable Real Estate: Multidisciplinary Approaches to an Evolving System" provides extensive analysis of how energy efficiency improvements, including high R-value insulation, impact property valuation in various markets.
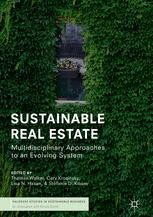
High R-value insulation delivers multiple benefits that extend far beyond simple energy conservation. From substantial financial savings to improved comfort, environmental impact reduction, noise dampening, and increased property value, the case for investing in quality insulation is compelling for UK homeowners.
Understanding U-value vs. R-value in insulation
- U-value measures heat loss through building elements; lower numbers mean better insulation
- R-value measures resistance to heat flow; higher numbers indicate better insulation
- They are mathematically inverse: U = 1/R
The fundamental difference between U-value and R-value
When discussing insulation performance, two key measurements come into play: U-value and R-value. These measurements approach thermal performance from opposite directions but work together to give a complete picture of insulation effectiveness.
R-value focuses on a material's resistance to heat flow. It tells you how well a specific insulation material blocks heat transfer. The higher the R-value, the better the material resists heat movement. In the UK, R-values are expressed in square meters Kelvin per Watt (m²K/W). This measurement is particularly helpful when selecting individual insulation materials since manufacturers list R-values on their products.
U-value, on the other hand, measures the rate of heat transfer through an entire building element such as a wall, roof, or window assembly. It accounts for all materials in the assembly and how they work together. U-values are expressed in Watts per square meter per Kelvin (W/m²K). Lower U-values indicate better insulation performance and less heat loss. Building regulations in the UK typically specify maximum allowable U-values rather than minimum R-values.
"While R-value measures a material's resistance to heat transfer, U-factor measures how much heat actually flows through a component or assembly. It's like measuring the actual leaks in your home's thermal envelope rather than only the strength of your barriers" Josh McIvor ThermaCote® UK
Mathematical relationship between U-value and R-value
The relationship between U-value and R-value is straightforward: they are mathematical inverses of each other. The formula is simple:
U = 1/R (or conversely, R = 1/U)
This inverse relationship means that as R-value increases, U-value decreases. For example, if an insulation material has an R-value of 5 m²K/W, the corresponding U-value would be 0.2 W/m²K (1 ÷ 5 = 0.2).
Understanding this relationship helps when comparing different insulation options or when building regulations specify requirements in terms of either U-value or R-value. For example, if UK building regulations require a wall to have a maximum U-value of 0.18 W/m²K, this translates to a minimum R-value of approximately 5.56 m²K/W (1 ÷ 0.18 = 5.56).
This mathematical relationship also explains why U-values are typically small decimal numbers (like 0.18 or 0.30), while R-values are usually larger whole numbers (like 3.3 or 5.56). Both are simply different ways of expressing the same thermal performance from opposite perspectives.
Practical applications in UK building standards
In the UK, building regulations and energy efficiency standards typically reference U-values rather than R-values. The current UK building regulations require specific maximum U-values for different building elements:
- New external walls: approximately 0.18 W/m²K
- Existing walls (when renovating): approximately 0.30 W/m²K
- Roofs: between 0.11 and 0.15 W/m²K depending on construction type
- Floors: between 0.13 and 0.22 W/m²K depending on construction type
These requirements translate into minimum R-values that insulation materials must provide. For example, a new external wall requirement of U-value 0.18 W/m²K means insulation with a combined R-value of at least 5.56 m²K/W is needed.
When assessing a property's energy efficiency, professionals often calculate U-values for the entire building envelope. This approach provides a more accurate picture of thermal performance than looking at individual material R-values alone, as it accounts for thermal bridging and the performance of the entire assembly.
U-values in window selection
Windows deserve special attention in the U-value vs. R-value discussion. For windows, U-values are particularly important and directly impact a home's energy efficiency. Modern high-performance windows in the UK typically have U-values between 0.8 and 1.6 W/m²K, significantly higher than wall U-values.
Windows are measured by U-value rather than R-value because of their complex construction. A window's thermal performance depends on multiple factors: the frame material, the number of glass panes, gas fills between panes, low-emissivity coatings, and the spacers between glass layers. The U-value provides a single number that captures the combined thermal performance of all these elements.
When replacing windows, paying close attention to U-values can significantly improve a home's overall thermal performance, especially in older properties where windows can be a major source of heat loss.
Calculating U-values and R-values for layered constructions
Real-world building elements rarely consist of a single material. Walls, for example, typically include multiple layers: external cladding, insulation, structural elements, and internal finishes. Each material contributes to the overall thermal performance.
For a multi-layered construction, R-values are additive. The total R-value is the sum of the R-values for each layer plus the surface resistance values. The formula is:
R-total = Rsi + R1 + R2 + R3 + ... + Rn + Rse
Where:
- Rsi is the internal surface resistance
- R1, R2, etc. are the R-values of individual material layers
- Rse is the external surface resistance
For each material layer, the R-value is calculated as:
R = thickness (in meters) ÷ thermal conductivity (λ, in W/mK)
For example, 15 cm (0.15 m) of glass wool insulation with a thermal conductivity of 0.035 W/mK provides an R-value of approximately 4.3 m²K/W (0.15 ÷ 0.035 = 4.3).
Once the total R-value is determined, the U-value is calculated by taking the reciprocal:
U-value = 1 ÷ R-total
This calculation process is essential for architects, builders, and insulation professionals to ensure that building designs meet thermal performance requirements and building regulations.
Making practical insulation decisions
Understanding both U-values and R-values helps homeowners make informed decisions about insulation upgrades. Here's how to apply this knowledge practically:
Start with building regulations: UK building regulations specify maximum U-values for different building elements. These provide minimum standards to meet.
Consider whole-element performance: Remember that the U-value represents the thermal performance of the entire building element. Adding insulation with a high R-value improves the overall U-value of the wall, roof, or floor.
Account for diminishing returns: As insulation thickness increases, the improvement in U-value becomes less significant. Doubling insulation thickness does not double thermal performance.
Balance cost and performance: Higher-performing insulation materials (with better R-values per unit thickness) typically cost more. Evaluate whether the improved thermal performance justifies the additional cost.
Consider space constraints: In renovation projects, space for additional insulation may be limited. Materials with higher R-values per unit thickness might be necessary even if they cost more. [Find out here how ThermaCote® performs with just 1mm of thickness]
For most UK homeowners, the practical approach is to focus on meeting or exceeding the U-values specified in building regulations. This typically requires installing insulation materials with R-values appropriate for the specific building element and construction type.
Advanced considerations for thermal performance
Beyond the basic understanding of U-values and R-values, several advanced factors affect real-world thermal performance:
Thermal Bridging occurs when more conductive materials create pathways for heat to bypass insulation. Common thermal bridges include wall studs, floor joists, and window frames. These can significantly reduce the effective R-value of an insulated assembly, resulting in a worse U-value than simple calculations might suggest.
Air leakage can bypass insulation entirely, allowing heat to escape through gaps and cracks. Even high R-value insulation performs poorly if air can flow around it. This is why air sealing is a critical complement to insulation.
Moisture Management affects insulation performance over time. Wet insulation has dramatically reduced R-value. Proper vapor barriers and ventilation are essential to maintain the designed thermal performance.
Dynamic Thermal Performance considers how building elements respond to changing conditions. Some materials with moderate R-values may perform better in real-world conditions due to thermal mass effects that moderate temperature swings.
Professional energy assessors use sophisticated software that accounts for these factors when calculating a building's energy performance. This produces more accurate predictions of energy use than simple R-value or U-value calculations alone.
For the most accurate assessment of a home's insulation needs, consider professional testing such as thermal imaging or blower door tests. These identify actual heat loss patterns and air leakage issues that simple R-value or U-value calculations might miss.
Common insulation materials for UK homes
- Different insulation materials offer distinct R-values and benefits for UK homes
- Mineral wool and fiberglass remain most popular due to cost-effectiveness
- Premium options like spray foam and PIR boards provide higher R-values for specific applications
Fibreglass insulation
Fiberglass insulation remains one of the most common choices for UK homes due to its balance of cost and performance. This material consists of fine glass fibers and typically comes in blanket form (also called batts) or as loose-fill. With an R-value of approximately 2.2 to 2.7 per inch (RSI 0.39-0.47), fiberglass provides good thermal resistance while being among the most affordable options on the market. For a standard 270mm loft installation, fiberglass can achieve R-values around R-30, meeting building regulations for roof spaces.
The popularity of fibreglass stems from its practical benefits beyond just thermal performance. Installation requires minimal specialized equipment, making it accessible for both professionals and competent DIY homeowners. The material is non-combustible, adding a safety element to its appeal.
However, fiberglass does have limitations that homeowners should consider. Its performance can decrease when wet, and proper handling during installation is essential since the glass fibers can irritate skin and respiratory systems. For this reason, protective equipment (gloves, masks, and eye protection) is essential during installation.
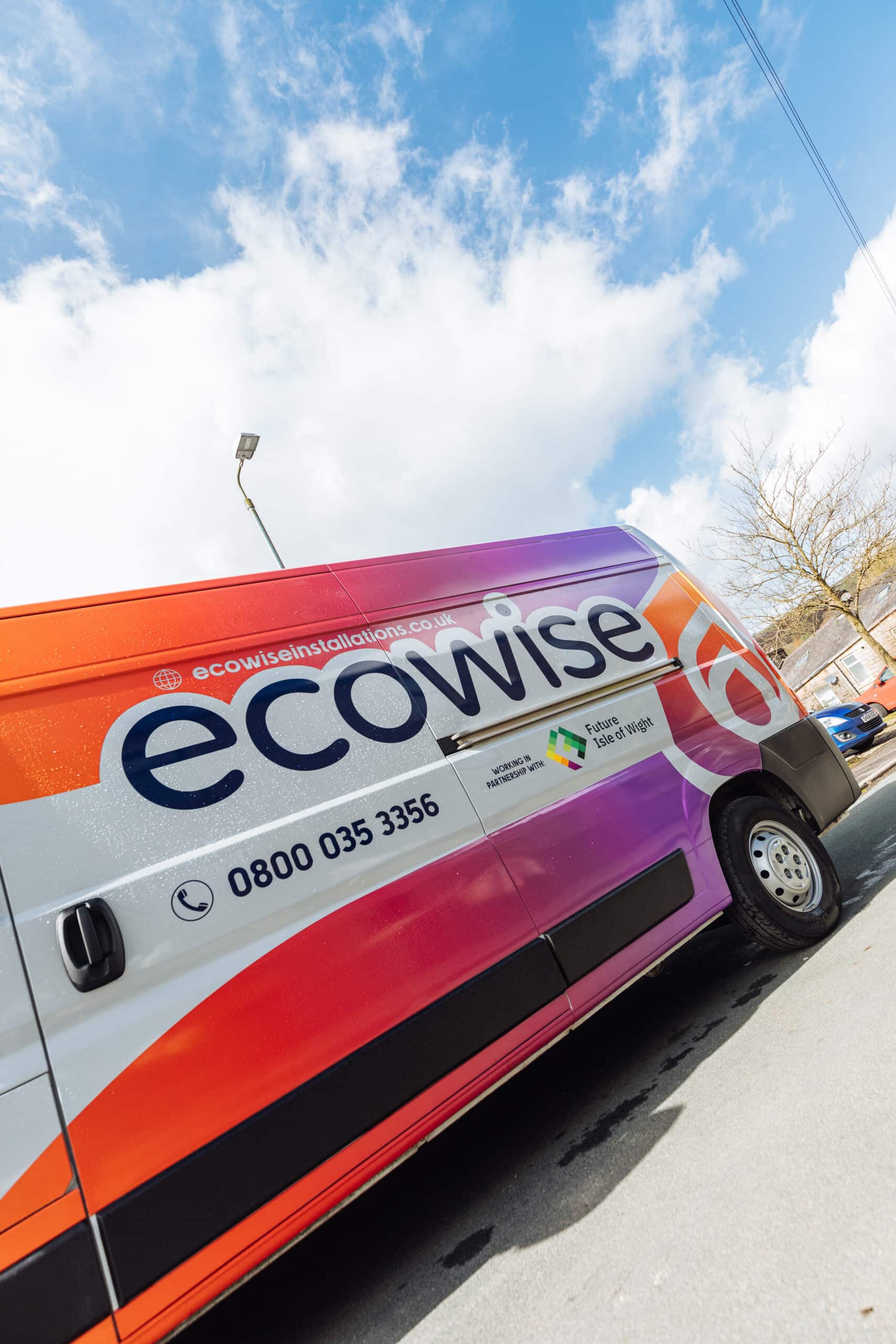
"The best cost versus effectiveness is found in mineral wool and fibreglass insulation. Both are relatively sustainable, affordable, and effective in thermal insulation. They are also quite versatile in their use and can be used in various home insulation projects," notes Akif from GreenMatch, highlighting the practical value proposition that keeps fiberglass among the top choices for UK homeowners.
Mineral wool insulation
Mineral wool, sometimes called rock wool or stone wool, represents another staple in UK home insulation. Made from molten rock, typically basalt or slag from steel mills, mineral wool offers thermal resistance similar to fiberglass with R-values between 3.0 and 3.3 per inch (RSI 0.53-0.58). This makes it slightly more effective than fiberglass while remaining in the affordable category of insulation materials.
The distinct advantages of mineral wool extend beyond pure thermal resistance. Its density provides excellent sound insulation properties, making it particularly valuable for homes in noisy areas or for interior walls between rooms. The material also offers superior fire resistance, with many products able to withstand temperatures up to 1000°C before deteriorating.
This provides crucial additional safety in the event of house fires. Mineral wool also handles moisture better than fibreglass, maintaining more of its insulating properties when damp, which suits the often wet UK climate.
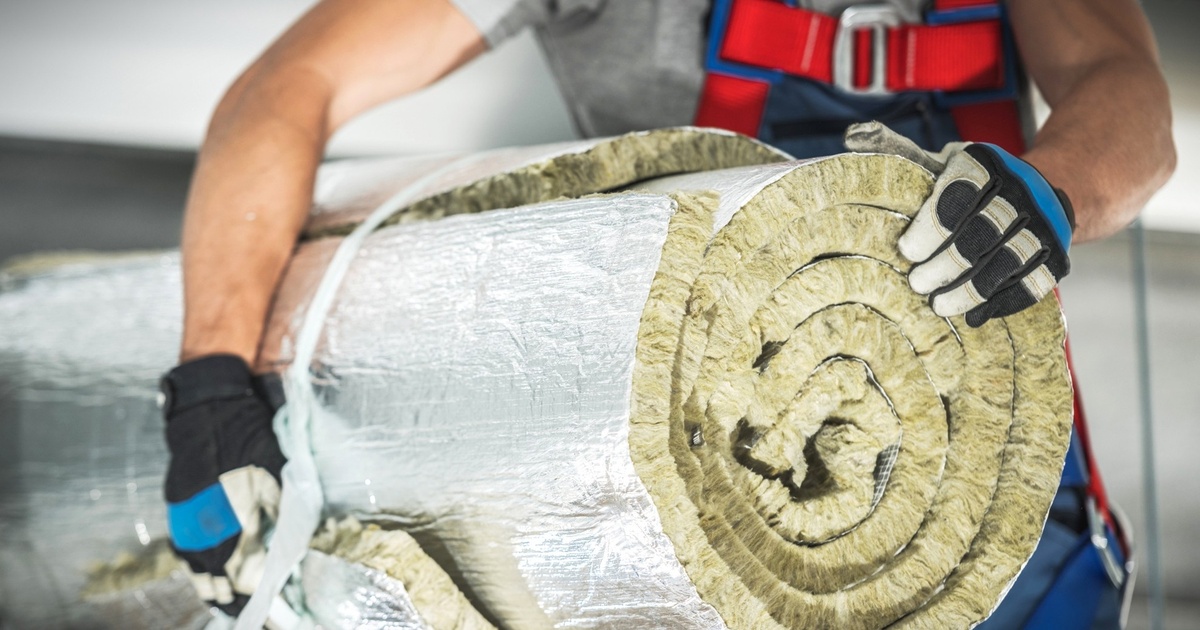
Understanding The Carbon Footprint of Rock Wool
For UK homeowners concerned about sustainability, mineral wool offers advantages worth considering. Most products contain 70-75% recycled content, and the material itself is recyclable at the end of its life cycle. This contrasts with many synthetic insulation materials that may end up in landfills. The practical applications for mineral wool in UK homes are diverse, from loft insulation to cavity walls and even external wall insulation systems. As GreenMatch notes, "For a loft space, mineral wool insulation is a safe bet that is affordable, effective, and easy to install."
Spray foam insulation
Spray foam insulation represents the premium end of the UK insulation market, offering significantly higher thermal resistance than traditional materials. Available in two main types – open-cell and closed-cell – this polyurethane-based material expands upon application to fill cavities and create an air-tight seal. Closed-cell spray foam achieves impressive R-values of 6.0 to 7.0 per inch (RSI 1.05-1.23), while open-cell provides around 3.5 per inch (RSI 0.62).
The performance advantages of spray foam extend beyond its high R-value. The material creates an effective air barrier, eliminating drafts and reducing heat loss through air movement. Closed-cell spray foam also forms a vapor barrier, controlling moisture migration through walls and roofs. This comprehensive approach to insulation can result in energy savings up to 50% compared to traditional insulation methods in some properties.
Despite these performance benefits, spray foam insulation requires careful consideration. The installation cost significantly exceeds that of mineral wool or fiberglass, often by 2-3 times. Installation must be performed by qualified professionals with specialized equipment, as improper application can lead to structural issues or reduced effectiveness.
The chemicals used during installation may also pose health concerns if proper ventilation isn't maintained during the curing process. For UK homeowners seeking maximum thermal efficiency in limited spaces, such as flat roof conversions or period properties with irregular wall cavities, spray foam's high R-value per inch makes it particularly valuable despite the higher cost.
Rigid board insulation
Rigid board insulation encompasses several high-performance synthetic materials that have become increasingly popular in UK construction and renovation. The most common types include polyisocyanurate (PIR), expanded polystyrene (EPS), and extruded polystyrene (XPS). PIR boards offer the highest R-values in this category, typically 5.6 to 8.0 per inch (RSI 0.98-1.41), making them particularly effective where installation space is limited.
PIR boards have become standard in many new UK construction projects and renovations due to their thermal efficiency. Their high R-value per thickness makes them ideal for floor insulation, flat roofs, and wall applications where space constraints exist. As noted by industry experts, "For a flat roof, you will require a robust option, such as PIR boards to withstand harsh weather conditions." The boards are relatively lightweight yet rigid, simplifying handling and installation while maintaining structural integrity.
Phenolic foam boards represent another high-performance option in rigid insulation, offering even higher R-values than PIR – up to 8.4 per inch (RSI 1.48). This makes phenolic boards the most thermally efficient conventional insulation material available in the UK market. As WhatCost experts highlight, "The insulation materials with the highest heat retention capability are phenolic boards and PIR boards. Both are synthetically made and boast remarkable heat retention and durability, making them a great choice for long-term comfort." While these premium rigid insulation boards come with higher initial costs, their exceptional thermal performance can result in faster payback through energy savings, particularly in properties with high heating demands.
ThermaCote® Thin Wall Insulation
ThermaCote® provides a radiant heat barrier in UK homes with some advantages not included in standard insulation.
Feature | Function in UK Homes |
---|---|
Radiant Heat Reflection | Reflects up to 85% of radiant heat, reducing surface heat gain/loss. Particularly effective on external walls, roofs, and internal ceilings. |
Thin, Spray-Applied Layer | Applied at ~1 mm thickness, so it doesn’t reduce living space or require major disruption—ideal for solid-walled, no-fines, or conservation area homes. |
Air & Moisture Barrier | Forms a semi-permeable membrane that reduces air leakage and helps regulate indoor temperature. Improves airtightness—important for Part L compliance. |
Breathable Surface | Unlike many vapor-sealed systems, ThermaCote is breathable, reducing condensation risk—a key factor in older UK housing stock. |
Internal or External Use | Can be applied inside (walls, ceilings) or outside (façades, soffits, roofs) depending on the retrofit strategy. |
Fire-Resistant & Durable | Class A fire rating, UV-stable, weatherproof—suitable for UK weather and compliant with BS 476 fire safety standards. |
Natural and eco-friendly insulation options
Natural insulation materials have gained popularity among UK homeowners concerned with environmental impact and indoor air quality. Sheep's wool insulation, with an R-value around 3.5 per inch (RSI 0.62), offers performance comparable to mineral wool while being renewable and biodegradable.
This material naturally regulates humidity, absorbing moisture when the air is damp and releasing it when conditions are dry – a valuable property in the UK climate.
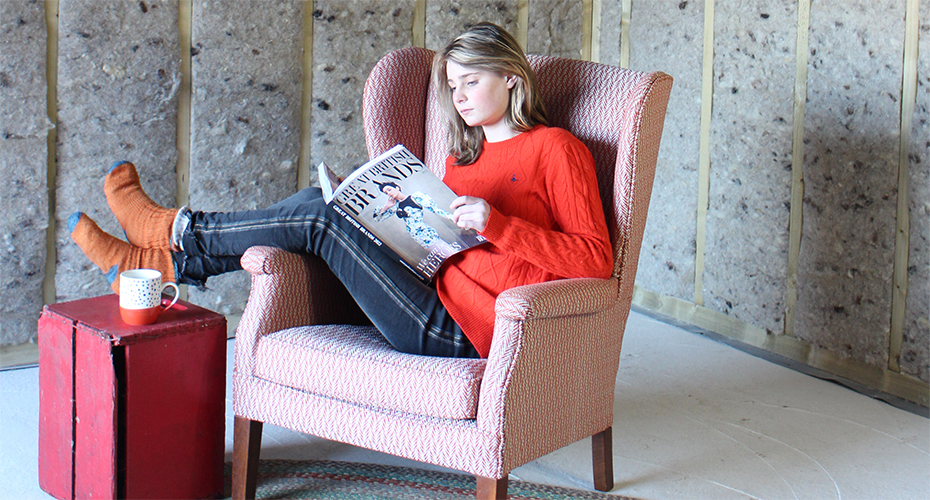
Wood fiber insulation boards provide another sustainable option, typically delivering R-values of 3.0-3.7 per inch (RSI 0.53-0.65). Manufactured from compressed wood fibers (often recycled), these boards offer good thermal and acoustic performance while having a significantly lower carbon footprint than synthetic alternatives. The material's density also provides thermal mass, helping to stabilize indoor temperatures during fluctuating external conditions.
Cellulose insulation, made from recycled paper treated with fire-retardant chemicals, offers an R-value around 3.2-3.8 per inch (RSI 0.56-0.67). This loose-fill material is particularly suitable for retrofitting existing UK homes, as it can be blown into wall cavities and loft spaces with minimal disruption. While these natural materials generally cost more than conventional fiberglass or mineral wool, they address growing consumer demand for reduced environmental impact.
University of Bath data show that natural insulation materials (like cellulose, straw, wool) commonly have more than 90% lower embodied energy/carbon per kilogram compared to synthetic insulations such as rigid polyurethane.

Comparative R-values and material selection considerations
The selection of insulation material for UK homes requires balancing thermal performance against practical constraints including budget, space limitations, and installation requirements. While R-value provides a standardized measure of thermal resistance, real-world performance depends on proper installation and addressing thermal bridges in the building envelope.
The performance differences between insulation materials become particularly significant when space constraints exist.
In older UK properties with solid walls, internal wall insulation that minimizes space loss becomes crucial. In these scenarios, high-performance materials like phenolic or PIR boards may justify their premium cost by preserving living space while delivering required thermal performance.
Improving energy efficiency with R-value
- Higher R-values mean better insulation performance and energy savings
- UK homes need specific R-values: 5.28-6.87 m²K/W for roofs, 3.30 m²K/W for walls
- Proper assessment and installation are just as important as choosing the right R-value
Step #1: Assess current insulation levels
The first step to improving your home's energy efficiency is understanding what you're working with. Most UK homes, especially older properties, have inadequate insulation that falls below current standards. Before adding new insulation, you need to know your starting point.
For DIY assessment, measure the thickness of existing insulation in different areas of your home. In the attic, use a ruler to check insulation depth between joists. For walls, you may need to check behind outlet covers or in unfinished areas. Once you have the thickness, check the material type (fibreglass, mineral wool, etc.) and use reference charts to determine the current R-value. Remember that R-value increases with thickness for the same material type.
Professional energy audits
For a more accurate assessment, consider hiring a professional energy auditor. These specialists use specialized equipment like thermal imaging cameras to identify heat loss areas and measure insulation effectiveness. Professional audits typically cost £200-£400 in the UK but provide detailed reports with specific recommendations.
A professional audit will reveal:
- Current insulation R-values in different parts of your home
- Areas with significant heat loss
- Air leakage points that reduce insulation effectiveness
- Customized recommendations based on your home's specific needs
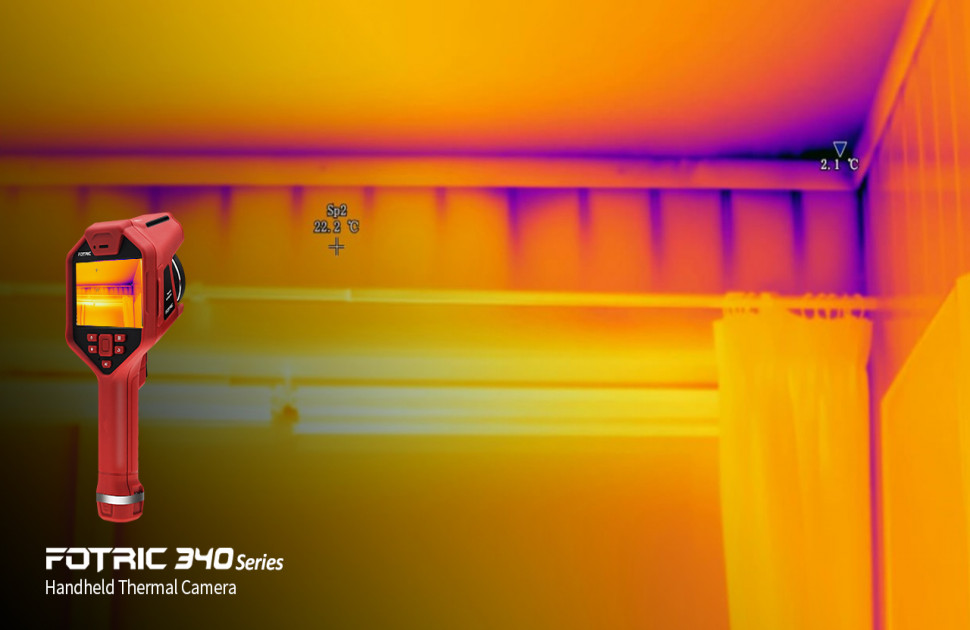
Using Thermal Cameras To Measure Heat Loss
Step #2: Choose the right insulation type
After assessing your current insulation, you'll need to select the appropriate insulation materials to reach your target R-values. For UK homes, aim for these minimum recommended values:
- Attics/roofs: 5.28-6.87 m²K/W (equivalent to R-30 to R-39 in imperial units)
- Walls: 3.30 m²K/W (equivalent to R-19 in imperial units)
- Floors: 2.29-5.28 m²K/W (equivalent to R-13 to R-30 in imperial units)
The right insulation type depends on your specific application area, budget constraints, and personal preferences. For attics, loose-fill insulation offers excellent coverage, especially in hard-to-reach spaces. For walls, consider blown-in insulation for existing walls or rigid foam boards for new construction.
Budget considerations
Consider the long-term value when selecting insulation. While spray foam insulation has a higher upfront cost, its superior R-value per inch (6.0-7.0) means you need less thickness to achieve the same thermal performance. This makes it ideal for space-constrained areas like flat roofs or narrow wall cavities.
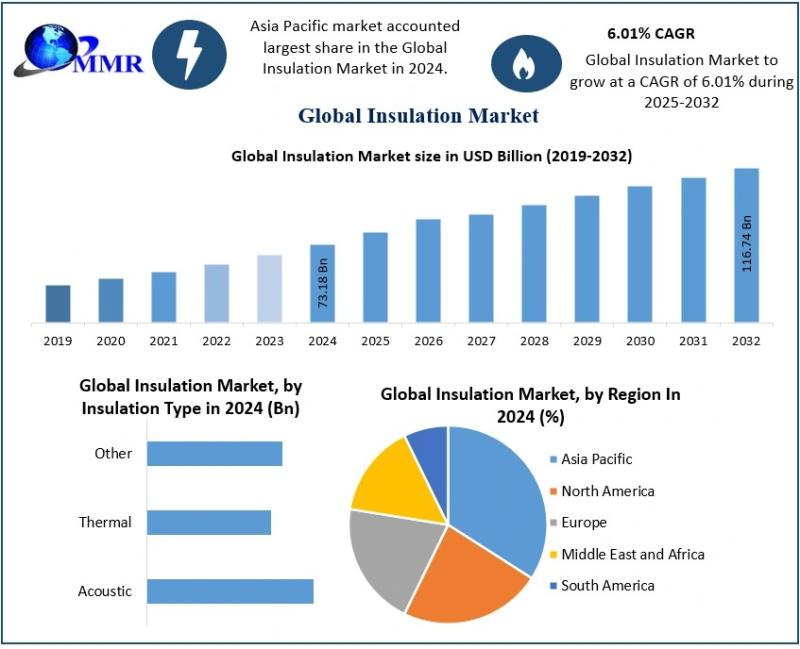
According to market data, the global insulation market was valued at USD 73.18 billion in 2024, with projected growth reflecting increasing demand for energy-efficient solutions. This growth is driving innovation and more cost-effective options.
Step #3: Calculate required insulation thickness
Once you've selected your insulation material, calculate how much you need to reach your target R-value. The formula is:
Required thickness = Target R-value ÷ R-value per inch of your chosen material
For example, if you want to achieve R-30 in your attic using mineral wool with an R-value of 3.3 per inch:
Required thickness = 30 ÷ 3.3 = 9.1 inches (approximately 23 cm)
Be sure to account for existing insulation if you're adding to what's already there. If you already have insulation with an R-value of 10, and you want to reach R-30, you need to add insulation with an R-value of 20.
Step #4: Prepare for installation
Proper preparation ensures maximum insulation effectiveness. Before installing new insulation:
1. Repair any roof or wall leaks that could damage insulation
2. Address ventilation needs (especially in attics and crawl spaces)
3. Ensure electrical wiring and fixtures are safe for contact with insulation
4. Install vapour barriers where needed to prevent moisture problems
5. Clear the area of debris and obstructions
For DIY installations, gather the necessary safety equipment: protective clothing, gloves, eye protection, and dust masks. When working with fiberglass or mineral wool, skin protection is essential to prevent irritation.
Professional vs. DIY installation
While DIY installation can save money, professional installation often provides better results. Professionals understand building science principles and can identify potential issues like thermal bridging (heat transfer through structural elements) that might reduce insulation effectiveness.
For complex installations like spray foam or for accessing difficult areas, professional installation is strongly recommended. The improved performance usually justifies the additional cost.
Step #5: Install insulation correctly
Proper installation is critical for achieving the rated R-value of any insulation material. Even small gaps or compressed areas can significantly reduce overall effectiveness.
For attic insulation:
- Lay batts perpendicular to joists to cover gaps
- Don't compress insulation as this reduces its R-value
- Ensure consistent depth throughout the space
- Leave proper clearance around recessed lights and other heat sources
- Don't block soffit vents that provide necessary ventilation
For wall insulation:
- Fill cavities completely without gaps or voids
- Cut batts to fit precisely around outlets, windows, and pipes
- Use expanding foam to seal small gaps around penetrations
- Install proper vapor barriers according to your climate zone
Tips for boosting R-value
Even with adequate insulation, your home's energy efficiency can be compromised by other factors. These tips help maximize the effectiveness of your insulation investment.
Air leakage can reduce insulation effectiveness by up to 50%. Before adding insulation, seal all gaps and cracks where air can enter or escape:
- Around windows and doors using weatherstripping
- Where pipes and wires enter the home using expanding foam
- Along baseboards and trim using caulk
- In attic hatches with weatherstripping and insulated covers
A blower door test can help identify less obvious air leaks. This test depressurizes your home and measures air infiltration rates, helping pinpoint areas needing attention.
Reflective barriers work differently from traditional insulation. Rather than slowing conductive heat transfer, they reflect radiant heat. In attics, installing radiant barriers on the underside of the roof can reduce summer heat gain by 10-25%.
For best results:
- Install with the reflective side facing an air gap
- Ensure proper attic ventilation remains in place
- Keep the reflective surface clean and dust-free
- Use in combination with traditional insulation, not as a replacement
Step #6: Monitor and maintain insulation performance
After installation, monitor your energy bills to track improvements. You should see reduced heating and cooling costs, especially during extreme weather. If savings aren't as expected, consider:
- Additional air sealing
- Addressing thermal bridges
- Adding insulation in overlooked areas
- Checking for settling or damage to existing insulation
Regular inspection helps maintain insulation effectiveness. Check annually for signs of moisture, pest damage, or settling, especially in attic spaces where insulation is visible.
What is a good R-value in the UK?
A "good" R-value depends on your location within the UK and the part of your home being insulated. For optimal energy efficiency in most UK climates:
- Roofs/attics: R-values above 4.54 m²K/W are recommended, with 5.28–6.87 m²K/W being ideal
- External walls: Aim for R-values between 2.29–3.70 m²K/W, with 3.30 m²K/W as a good target
- Floors: R-values between 2.29–5.28 m²K/W provide good performance
These values exceed minimum building regulations in many cases but provide better energy efficiency and comfort. In colder northern regions like Scotland, consider the higher end of these ranges. In milder southern areas, the lower end may be sufficient.
Understanding R-value diminishing returns
While higher R-values always improve insulation performance, there's a point of diminishing returns. Doubling insulation from R-10 to R-20 cuts heat loss by 50%, but going from R-20 to R-30 only reduces it by an additional 17%.
This doesn't mean you should skimp on insulation, but rather that you should prioritize areas with the lowest existing R-values first. If your attic already has R-25 insulation but your walls are only R-5, improving the walls will yield greater energy savings than adding more to the attic.
Energy efficiency improvements through proper insulation go beyond comfort and cost savings. They represent a significant step toward reducing carbon emissions. When homes require less energy for heating and cooling, their environmental impact decreases proportionally.
How does home insulation work?
- Insulation creates a thermal barrier that slows heat transfer in and out of your home
- Effective insulation tackles all three heat transfer methods: conduction, convection, and radiation
- Proper installation is just as important as the R-value for achieving energy efficiency
The science of heat flow
Heat naturally moves from warmer areas to cooler ones. In winter, heat from your home tries to escape to the colder outside. In summer, outdoor heat attempts to enter your cooler home. Insulation works by creating resistance to this natural heat flow.
When installed correctly, insulation forms a thermal barrier between your home's interior and the external environment. This barrier significantly reduces the rate at which heat transfers through your walls, floors, and ceiling. The effectiveness of this barrier is measured by its R-value – the higher the R-value, the greater the resistance to heat flow and the better the insulation performs.
"Insulation serves as a barrier to heat transfer, helping to maintain indoor temperatures and reduce the energy needed for heating or cooling," according to industry experts. This fundamental principle explains why properly insulated homes require less energy for heating and cooling, leading to lower utility bills and reduced environmental impact.
- Check your home for thermal bridges (areas where heat escapes easily) like window frames, door frames, and where walls meet floors
- Consider supplementing existing insulation if you notice temperature inconsistencies in different rooms
- Use a thermal imaging camera (rentable from many hardware stores) to identify areas of heat loss
Understanding the three types of heat transfer
Effective insulation must address all three mechanisms of heat transfer: conduction, convection, and radiation. Each works differently, and various insulation materials tackle them in different ways.
Conduction: Heat traveling through solid materials
Conduction occurs when heat moves directly through a material, similar to how a metal spoon gets hot when left in a warm soup. Most insulation materials work primarily by disrupting conduction. They contain millions of tiny pockets of air or gas that break up the path heat would take. Since air is a poor conductor of heat, these pockets significantly slow down heat transfer.
Fibrous materials like fibreglass and mineral wool trap air between their fibers. Foam insulations like polyurethane and polystyrene contain tiny gas-filled cells. The effectiveness of insulation against conduction is directly measured by its R-value – the higher the R-value, the better it prevents conductive heat transfer.
Convection: Heat carried by moving air
Convection happens when heat travels via the movement of liquids or gases. In homes, this often means warm air rising and cool air sinking, creating currents that can bypass insulation if not properly addressed.
Dense insulation materials and proper air sealing work together to minimize convective heat loss. Without addressing air leakage, even high R-value insulation can underperform. Spray foam insulation excels at reducing convection because it creates an air seal in addition to providing thermal resistance.
Radiation: Heat traveling as infrared energy
Radiation transfers heat through electromagnetic waves and doesn't require a physical medium. The sun warms the earth through radiation, and similarly, warm objects in your home emit infrared radiation that can pass through some materials.
Reflective insulation and radiant barriers specifically target radiative heat transfer. These materials, often with shiny aluminum surfaces, reflect radiant heat rather than absorbing it. They're particularly effective in hot climates where cooling costs dominate, especially when installed in attics to reflect the sun's heat.
- Address all three heat transfer types when planning insulation upgrades
- Consider adding a radiant barrier in your attic if you live in a hot climate
- Ensure proper air sealing before adding new insulation to maximize effectiveness
The year-round benefits of proper insulation
A common misconception is that insulation only matters in winter. In reality, insulation works throughout the year to maintain comfortable indoor temperatures and reduce energy consumption.
During winter months, insulation keeps expensive heated air inside your home, reducing the workload on your heating system. The thermal barrier prevents the warmth from escaping through your walls, roof, and floors. This is especially important in the UK, where heating costs represent a significant portion of household energy bills.
In summer, the same insulation prevents outdoor heat from infiltrating your home, keeping interiors cooler and reducing the need for air conditioning or fans.
Beyond temperature control, insulation also provides acoustic benefits by reducing the transmission of sound between rooms and from outside. This creates a quieter, more peaceful living environment throughout the year. Additionally, proper insulation helps control moisture movement through your building envelope, which can protect against mould and structural damage in the UK's often damp climate.
- Review your insulation performance in different seasons to identify improvement opportunities
- Consider upgrading attic insulation first, as it provides the greatest year-round benefits
- Remember that insulation works for both keeping heat in and keeping heat out
The critical role of proper installation
The best insulation materials can fail to deliver their rated R-values if improperly installed. Installation quality directly impacts insulation performance and can make the difference between an energy-efficient home and one that wastes energy despite having insulation in place.
Common installation problems include compressed insulation, gaps and voids, and thermal bridging. When fiberglass or mineral wool insulation is compressed to fit into a smaller space than designed for, its R-value decreases significantly. Air gaps between insulation sections or around fixtures create pathways for heat to bypass the insulation.
Thermal bridges occur where building materials with poor insulation properties (like wood studs or metal fasteners) create direct paths for heat to travel through the insulation layer.
Professional installation often delivers better results, particularly for technically challenging materials like spray foam. However, many homeowners successfully install certain types of insulation themselves, such as laying additional rolls in the attic. Whether professional or DIY, following manufacturer guidelines and building regulations is essential.
Different insulation types require specific installation techniques. Batt insulation must be cut precisely to fit around obstacles and fill cavities completely. Loose-fill insulation needs to be blown in at the correct density. Rigid board insulation requires proper sealing at joints.
Spray foam or thin wall insulation must be applied at the right thickness and temperature conditions for optimal curing.
- Inspect existing insulation for compression, gaps, and settling
- When installing new insulation, follow manufacturer specifications precisely
- Consider a blower door test to identify air leakage that might compromise insulation performance
How to choose the best insulation for your UK home
- Find the right insulation based on your specific home needs
- Balance cost, climate factors, and property type for optimal results
- Learn when to DIY and when to call professionals
Selecting the right insulation for your UK home isn't only about picking the highest R-value product. Several factors should guide your decision to ensure you get the best thermal performance for your specific situation. Let's examine the key considerations that will help you make an informed choice.
Consider your local climate
The UK's climate varies significantly from the mild southwest to the harsh winters of Scotland. These regional differences directly impact your insulation needs and the optimal R-value required for your home.
Weather patterns across the UK show notable variations in temperature, rainfall, and wind exposure. Homes in Scotland may need insulation with higher R-values (around 5.0-6.0 for walls) compared to properties in southern England (where R-values of 3.5-4.5 might suffice).
According to the Energy Saving Trust, homes in northern regions can lose up to 15% more heat than those in southern areas, highlighting the importance of climate-appropriate insulation.
The exposure of your property matters too. Coastal homes face different challenges than inland properties. Homes near the coast experience higher humidity levels and stronger winds, which can affect insulation performance. For these properties, moisture-resistant insulation materials like closed-cell spray foam or certain types of rigid board insulation often perform better than traditional options like fibreglass.
Matching insulation to seasonal demands
Your home must handle both winter cold and summer heat. In winter, good insulation prevents heat escape, while in summer, it keeps heat out. For UK homes that experience both hot summer days and cold winters, materials with stable R-values across temperature ranges are ideal. PIR (polyisocyanurate) boards maintain their thermal resistance better across temperature variations compared to some other options.
Evaluate the cost-benefit
Insulation represents a significant investment in your home, but the returns can be substantial. The key is finding the right balance between upfront costs and long-term energy savings.
Initial insulation costs vary widely based on material choice and installation method. Basic loft insulation might cost £300-£400 for a typical semi-detached house, while full external wall insulation could run £8,000-£15,000. However, these costs should be viewed against potential savings. According to the Energy Saving Trust, proper loft insulation can save approximately £150-£250 per year on heating bills, while wall insulation might save £100-£375 annually depending on your property type.
The payback period—the time it takes for energy savings to cover the initial investment—varies by insulation type. Loft insulation typically pays for itself within 1-2 years, making it an obvious first choice. Cavity wall insulation might take 3-5 years, while solid wall insulation could take 10-15 years to recoup costs. However, with rising energy prices, these payback periods are shrinking, making even more expensive insulation options financially sensible.
Might be good to include a TC cost comparison inhere to show our value vs other systems
Factoring in property value increases
Quality insulation doesn't only save on bills—it adds value to your property. Homes with high energy efficiency ratings (EPC ratings) typically command higher prices. Data from the Department of Energy suggests that moving from EPC band D to band B could increase your property value by an average of 6%. For a £250,000 home, that's a £15,000 increase, often exceeding the cost of the insulation itself.
Consult with professionals
Professional guidance can be invaluable when selecting and installing insulation. Experts can identify your home's specific needs and recommend appropriate solutions.
A professional energy assessment provides insights that DIY evaluations might miss. Energy assessors use specialized equipment like thermal imaging cameras to identify heat loss points in your home. They can determine your current insulation levels and pinpoint areas needing improvement. This targeted approach ensures you invest in insulation where it will have the greatest impact.
When seeking professional advice, look for contractors with proper credentials. In the UK, insulation installers should be registered with organizations like the National Insulation Association (NIA) or be TrustMark approved. These credentials ensure they follow industry standards and best practices. Always check references and past work when selecting an installer.
Questions to ask potential installers
When interviewing insulation professionals, ask specific questions to gauge their expertise:
- What R-value do you recommend for my specific property and why?
- How will you handle existing problems like condensation or mold?
- What measures will you take to prevent thermal bridging?
- How will you ensure proper ventilation after insulation is installed?
- What warranties do you offer on materials and installation?
These questions help ensure the contractor understands the science behind insulation and isn't only trying to sell you the most expensive option.
Maintenance and upgrades
Insulation isn't a one-time installation that lasts forever. Regular checks and occasional upgrades are essential to maintain its effectiveness over time.
Insulation performance can degrade for various reasons. Water damage from roof leaks can reduce the effectiveness of loft insulation. Settling in loose-fill insulation can create gaps where heat escapes. Pests might damage some insulation materials. Regular visual inspections can help identify these issues before they significantly impact your home's thermal performance.
For older homes with existing insulation, upgrades can dramatically improve energy efficiency. If your home was insulated to older standards (pre-2000s), it likely has lower R-values than currently recommended. Adding a new layer of insulation over existing materials can be a cost-effective way to boost thermal performance without complete replacement.
Signs your insulation needs attention
Watch for these indicators that your insulation may need maintenance or replacement:
- Unusually high energy bills compared to similar properties
- Rooms that feel drafty or have fluctuating temperatures
- Walls that feel cold to the touch in winter
- Ice dams forming on your roof during cold weather
- Excessive heat in upstairs rooms during summer
If you notice these signs, a professional inspection can determine whether simple repairs or complete replacement is needed.
Retrofitting older properties with modern insulation materials often presents unique challenges. Original features like cornices or wooden floors might complicate installation. In these cases, specialists in period property insulation can suggest solutions that improve energy efficiency while preserving architectural details.
Materials like aerogel insulation, though more expensive, can provide high R-values with minimal thickness, making them ideal for retrofitting historic buildings where space is limited.
Over To You
Proper insulation with the right R-values isn't only about ticking boxes for energy regulations—it's about creating a home that truly works for you. When you understand R-values, you gain control over your living space, your comfort, and your energy bills. For UK homeowners, this knowledge translates directly to warmer winters, cooler summers, and significantly reduced energy costs.
Remember that R-values aren't one-size-fits-all. Your home's needs depend on its location, construction, and your personal comfort preferences. Whether you're focusing on attic insulation at R30-R44 or wall insulation at R13-R23, these numbers represent real comfort and savings in your daily life.
As energy costs continue to rise across the UK, proper insulation becomes not only a smart choice but a necessary one. By taking steps to assess your current insulation, choosing the right materials, and working with qualified professionals, you're making an investment that pays dividends in both comfort and cost savings for years to come.
Your home deserves the best protection against the elements—and now you know exactly how to provide it.